10
2022
-
07
Aluminum welding flux is a flux used during aluminum welding.
Author:
Aluminum soldering agentUsage: Used for aluminum wire and copper. Aluminum wire andWelded into iron, stainless steel.
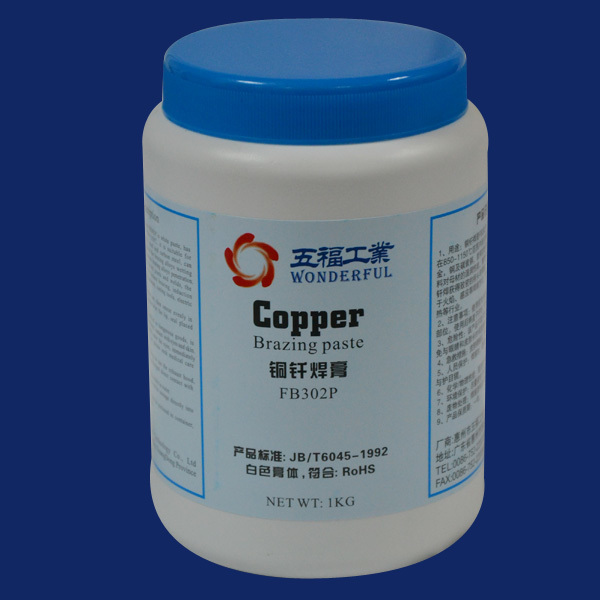
Applicable range of soldering agent: Suitable for the production of various high and low transformers, power distribution boxes, lighting distribution boxes, high-power regulators, high-precision fully automatic regulators, isolated transformers, motors, etc.
Soldering agent
Application method of soldering agent: First clean the surface to be soldered, applyAluminum soldering agentand then it can be soldered.
Precautions for soldering agent: 1. If there are residues after soldering, they can be wiped clean with wet wipes. 2. Soldering temperature of 330 degrees Celsius. Performance: flame retardant, non-toxic, non-corrosive.
Industries using flux:
The soldering agent is a viscous liquid; what is its main use? Knowing the range of application is important. Allow me to introduce the general application range of aluminum soldering agents.
Aluminum soldering agent is a welding material based on lead-tin that welds aluminum, aluminum alloys with copper, steel, copper alloys, and other metals together; it is an indispensable welding material. It can be used in the electronics industry for aluminum enameled wire and in the lighting industry for aluminum lamps. Its main function is to remove the oxide film on the metal surface and increase the wettability of the solder on the metal surface, thus allowing the solder to bond with the metal substrate.
The wettability and bonding strength between solder materials and aluminum are related to the composition of the solder materials and the silicon and magnesium content in aluminum. Zinc can increase the wettability of surface solder. It is difficult to weld aluminum alloys with high magnesium and silicon content using lead-tin solder materials.
Classification:
Different soldering agents have different effects when used. It mainly depends onAluminum soldering agentthe type; soldering agents can be classified into various types. What are the differences? Below is a brief introduction to the classification of aluminum soldering agents.
There are various types of soldering agents with diverse effects; based on the functions and roles of additives, they can be divided into five categories: crosslinking agents, process additives, etc.
Soldering agents can be divided into several parts based on their functions:
1. Optimizing processing performance: lubricants, depilatory agents, stabilizers, processing aids, thixotropic agents, etc.
2. Optimizing mechanical performance: plasticizers, reinforcing fillers, enhancers, impact modifiers.
3. Optimizing optical performance: pigments, dyes, nucleating agents, fluorescent whitening agents.
Industries using flux:
The soldering agent is a gelatinous viscous liquid; what are its main functions? How much do you know about its application range? First, let me introduce the general application range of aluminum soldering agents.
The soldering agent is a welding material based on lead-tin that welds aluminum alloys and serves as a basic solder for welding aluminum with copper, steel, copper alloys, and other metals. It can be used in the electronics industry for aluminum enameled wire, boards, and lamp sockets. Its main function is to remove the oxide film on metal surfaces and increase the wettability of welding materials so that they can bond with metals during gas welding.
The wettability and bonding strength between welding materials and aluminum are related to the composition of welding materials and the silicon and magnesium content in aluminum. Zinc can enhance surface wettability of welding materials. However, it is challenging to weld aluminum alloys with high magnesium and silicon content using lead-tin welding materials. Flux classification:
Different solvents have different effects when used; it mainly depends on the type of solvent. Then based on type, solvents can be classified into several categories. What are the differences? First, let’s briefly introduce the classification of aluminum solvents.
There are various types of soldering agents with diverse effects; based on the functions and roles of additives, they can be divided into five categories: crosslinking additives and process additives.
Soldering agents can be divided into:
1. Processing performance optimization: lubricants, depilatory agents, stabilizers, processing aids, thixotropic agents.
2. Optimizing mechanical performance: plasticizers, reinforcing fillers enhancers, impact modifiers.
3. Optimizing optical performance: pigments, dyes, nucleating agents and fluorescent whitening agents.
Aluminum welding agent, brazing agent, aluminum brazing agent, brazing materials
Previous Page
Previous Page
10
2022-07
Aluminum welding flux is a flux used during aluminum welding.
30
2022-06
Aviation brazing materials are developing towards lower costs.
29
2022-06
The task control center plays an important role in handling soldering materials.
20
2022-06
Brazing process solutions, brazing equipment consulting, advanced brazing materials
15
2022-06
Selection of Gas Shielded Welding Wire - Flux-Cored Wire
08
2022-06
How to choose welding wire for gas shielded welding of steel?
28
2022-05
Types of gas shielded welding wires
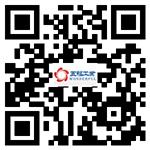
Huizhou Wonderful Industrial Technology Co., Ltd.
Address: Yunshan West Road, Huicheng District, Huizhou City, Guangdong Province
Telephone:+86-752-2893501 +86-752-2200396
Website:www.cnwufu.com
E-mail:sales@cnwufu.com