25
2021
-
09
A more environmentally friendly and energy-saving soldering agent spraying device
Author:
Currently before brazingFluxThere are basically two types of spraying: spraying and powder spraying. The overall structure of powder spraying generally adopts a hanging spraying method, which means that the plates to be sprayed are suspended at the spray gun's outlet. The flux powder is adsorbed onto the spray gun through an electrostatic powder suction device, and then sprayed through the spray gun. In this flux spraying method, due to the equipment layout on the assembly line, it occupies a large area, and the entire powder spraying system is bulky. Additionally, the hanging assembly line cannot meet the spraying requirements for large-area plates; most aluminum plates do not have hanging parts and require special hanging components. Due to gravity and unreasonable positioning of the spray gun, it is easy to cause uneven spraying in the vertical direction of the plates, resulting in thinner upper layers compared to lower layers. Any slight vibration can cause powder to fall off, making it difficult to effectively control the thickness of the powder layer.
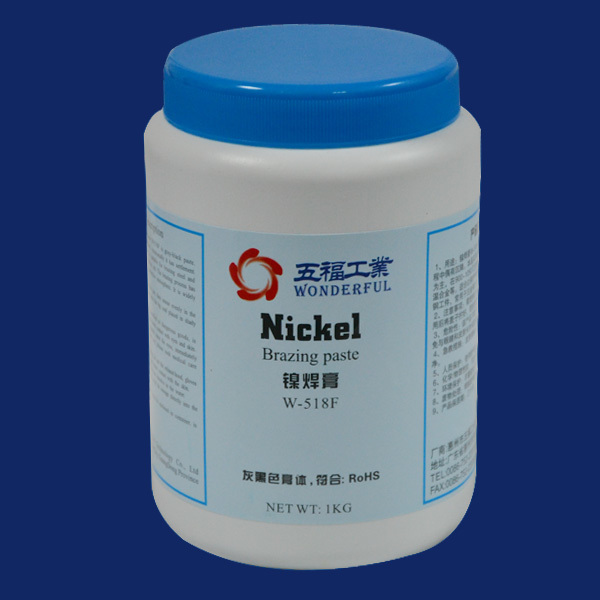
In order to overcome existingFluxshortcomings of spraying technology, technicians have provided a more environmentally friendly and energy-saving flux spraying device. It is realized through the following technical solutions. A flux spraying device includes a horizontal conveying system for transporting plates to be sprayed, with uniform gaps at the bottom of the conveying system; the spraying system includes an outer frame body and a spray gun set inside the outer frame body. The outer frame body is fixedly arranged above the conveying system, forming an upper cover for the conveying system, effectively preventing powder leakage and dust pollution in the working environment; a powder supply system is used to output flux powder to the spraying system; a powder recovery system is set at the bottom of the conveying system, communicating with the gaps of the conveying system, used to collect flux powder that has not been sprayed onto the plates.
Among them, attention should be paid when making this flux spraying device: an induction sensor is set at the feed inlet at the front end of the conveying system. It includes a control system connected with sensors, spray guns, and conveying systems, used to control the conveying speed of the conveying system and the speed at which powder is ejected from the spray gun. The spray gun is fixedly installed on a reciprocating system. The reciprocating system includes a mechanism frame, a belt drive wheel mechanism, and a spray nozzle bracket fixedly mounted on a second belt of the belt drive wheel mechanism. The upper part of the powder recovery system is connected to the conveying system through a funnel-shaped recovery guide plate. The power supply system is sealed in an electrical box. A vibrating motor is set in the powder supply system for fluidizing powder. The main body of the outer frame includes a skeleton and sealing plates; the skeleton is connected by welding, and sealing plates are fixed on the skeleton with nails, with seams sealed by sealing glue.
ThisFluxspraying device has the following technical effects: 1. Due to adopting a new type of assembly line device, powder is recovered by gravity; since the spraying system is set above the plates to be sprayed and they are placed horizontally, it can effectively overcome gravity's influence for more uniform spraying; its up-and-down structural design makes it more compact and occupies less area while being able to spray various specifications of plates with higher versatility; 2. The conveying speed of the conveying system and operating speed of the reciprocating system are controlled by a control system, which can effectively control spraying thickness while also reducing labor costs and improving work efficiency; 3. The upper part of the spraying system has a hood-shaped outer frame body that can effectively reduce dust in the working area, achieving pollution-free operation.
Gas shielded welding wire, aluminum welding flux, brazing agent, aluminum brazing flux, brazing materials
10
2022-07
Aluminum welding flux is a flux used during aluminum welding.
30
2022-06
Aviation brazing materials are developing towards lower costs.
29
2022-06
The task control center plays an important role in handling soldering materials.
20
2022-06
Brazing process solutions, brazing equipment consulting, advanced brazing materials
15
2022-06
Selection of Gas Shielded Welding Wire - Flux-Cored Wire
08
2022-06
How to choose welding wire for gas shielded welding of steel?
28
2022-05
Types of gas shielded welding wires
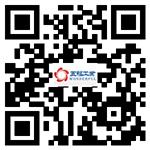
Huizhou Wonderful Industrial Technology Co., Ltd.
Address: Yunshan West Road, Huicheng District, Huizhou City, Guangdong Province
Telephone:+86-752-2893501 +86-752-2200396
Website:www.cnwufu.com
E-mail:sales@cnwufu.com